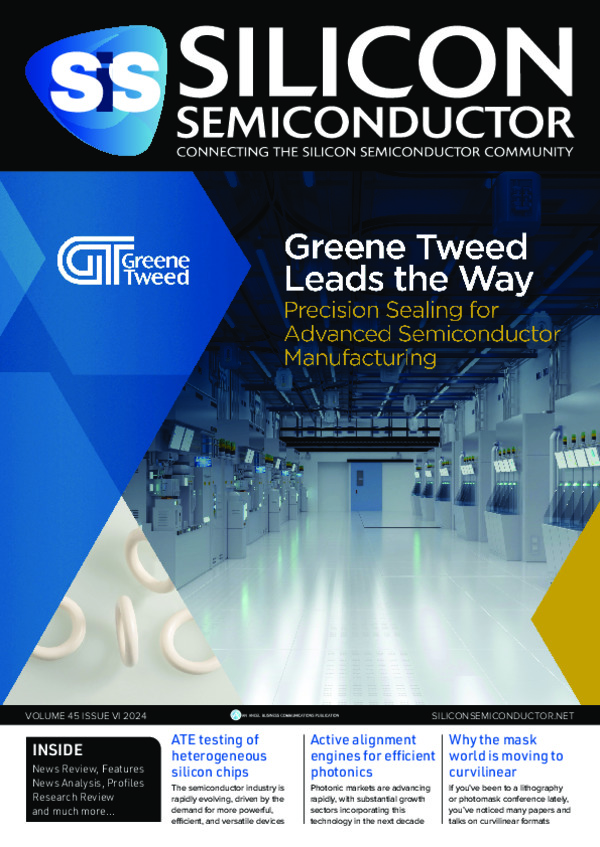
Advanced thermal control techniques to improve wafer manufacturing yield
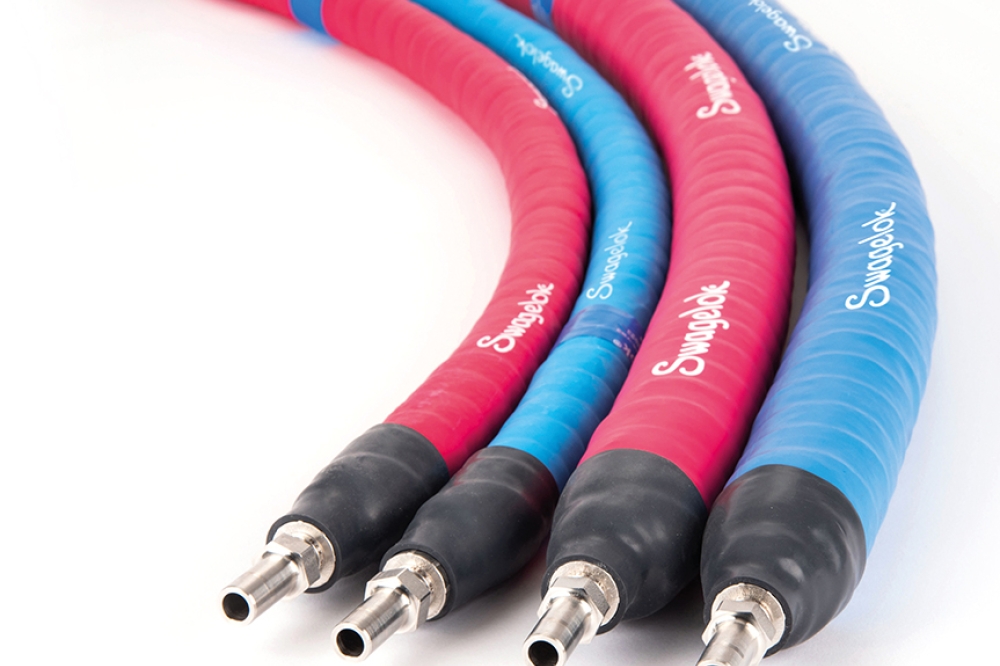
Finding hoses with proper insulation can mean the difference between success and failure.
By Margaret Brennan, Principal Engineering Lead, Application Solutions, Swagelok Company
Demand for high-quality semiconductor wafers has grown exponentially as artificial intelligence and other technological advances require more sophisticated chips. The process of creating the chips has never been more complex, and fabrication plants, OEMs, and all parts of the value chain are seeking new ways to maximize efficiency and improve profitability.
To maximize chip yield, the thermal loop is designed to keep chambers at optimal temperatures throughout the manufacturing process. Ultralow temperatures are often used to regulate precise temperatures in the chamber for etch processes, where as deposition process see much higher temperature. The challenge is that these temperatures put additional pressure on each component of the thermal loop. This critical loop can consist of chillers, pumps, heat exchangers, and all the components that keep them connected. A single malfunctioning component within that system can reduce fab efficiency and output.
Precision and cleanliness are also intersecting priorities in the world of semiconductor chip production. Temperatures inside the tool chamber must be kept at optimized levels to ensure process stability. Simultaneously, the chamber must be kept entirely free of potential contaminants to maximize the throughput of chips during the delicate fabrication process.
Because significant engineering and design go into creating and maintaining an ideal fabrication environment, it can be easy to overlook the importance of selecting some of the more “basic” components that support the chip production process. Consider an industrial hose, which is used in countless applications throughout manufacturing facilities. In the semiconductor fabrication process, hoses play an important role, as they are commonly used to help the chillers and heat exchangers regulate the environment necessary for production processes.
Getting hoses and other system components right means paying attention to three critical areas that affect how components will function in the thermal loop, including:
• Choosing the right components
• Finding the right insulative balance
• Using proper installation and performance testing
Before constructing a thermal loop for a semiconductor wafer fab, it is crucial to understand the importance of optimal temperature control. Finding suppliers who can guide engineers through this critical area and support the design and implementation of thermal loop construction will help fabricators optimize thermal management and maximize the number of high-quality chips produced.
Figure 3. Selecting the right insulated hose is critical to mitigating
condensation issues in fab production operations and may involve
selecting vacuum-insulated metal hoses, which provide excellent
insulation against extreme media temperatures.
How to keep fluid temperatures stable
Keeping temperatures at precise levels in the chamber is essential to produce the highest-quality semiconductor chips. To regulate them, powerful chillers pump temperature - cooling media into and out of the machine. The hoses that transfer this media must be properly insulated, when necessary, to ensure temperatures remain stable throughout the fabrication process.
For example, if the natural temperature change that occurs as fluid moves through the system is not accounted for when determining the cooling/heating temperature and amount of insulation needed, it can cause out-of-tolerance temperature
fluctuations within the chamber. These fluctuations may result in wafer defects, which can reduce yields.
In cold applications, semiconductor manufacturers often times use water containing glycol to prevent freezing because it can withstand temperatures as low as -40°C. It is energy intensive to keep temperatures ultralow, so using insulated industrial hoses can help fabricators control temperatures more effectively. Semiconductor manufacturers are particularly sensitive to keeping the temperatures at precise levels to produce high-quality chips and keep energy costs down. The same goes for hot applications, with the additional concern of safety where surface temperatures of components must remain safe to touch.
Choosing the right components
With temperature management during semiconductor manufacturing being essential, system designers must specify the right components to build a thermal loop that can withstand harsh operating conditions. Each component—hoses, valves, fittings, filters, and more—must meet the minimum requirements, including handling modern pressure and flow rates in addition to extreme temperatures (Figure 1).
Thermal loop hoses represent a particularly critical example because of the need for insulation (Figure 2). Enabling greater equipment efficiency with insulated hoses will keep temperature variations to a minimum, reduce heat transfer, and prevent condensation. Selecting components with these characteristics can help keep the fab running more efficiently and reduce overall downtime.
Though condensation is a threat to most industrial applications, it can halt production in a fab. In addition to dripping water potentially damaging critical equipment, unidentified leaks or puddles are always assumed to be toxic, which requires evacuation until the media is identified and determined to be safe. This unnecessary downtime and resource allocation can hinder a facility’s chip production, which is why having properly insulated hoses is critical (see Figure 3).
Finding the right insulative balance
The solution for proper thermal performance is more complex than simply adding insulation to components. The longer the length of the hose, the more insulation is necessary, which can become costly. Therefore, installing the optimal amount of insulation will enhance the system’s efficiency and minimize unnecessary costs.
A study of a fab’s thermal loop system was conducted to demonstrate the efficiency gains that properly insulated hoses can provide. The tool needed -30°C chilled water to achieve the desired temperature in the etch process. To do this, the chiller upstream had to supply temperatures colder than -30°C so that the media would land at -30°C by the time it entered the tool. In this case, the tool was 40 feet away from the chiller.
Had an uninsulated hose been used to transport media across this distance, the chiller would have needed to provide much colder temperatures than it would if hoses were insulated because of the cooling loss (or heat gain) that would occur during the media’s journey to the tool.
Figure 4. Be careful not to bend insulated hoses too much to avoid crimping the hose and affecting the insulation properties.
This overworks the chiller, leading to excessive energy costs, higher maintenance frequency, and possibly a shortened equipment life cycle. With an insulated hose, the chiller can provide temperatures closer to -30°C because it won’t need to overcompensate as much for any cooling lost throughout the transport to the tool. In this example, every reduction of 1°C costs about 27 cents (USD) per hour. Saving 44 degrees of chilling requirements, for example, could save $11.80 (USD) per hour in cooling costs.This can quickly add up once you multiply this cost by the number of chillers in the fab and number of hours they run per day. While insulated hoses cost more, they can pay for themselves in energy savings.
Proper installation techniques and performance testing
Once designers and engineers choose the right components to maintain effective thermal management, the next step to building a high-performance system is the installation and implementation of those components. It is crucial to follow these protocols precisely to ensure each system is installed consistently, repeatably, cleanly, and moisture-free.
Review the basics before starting to install a system in the fab. As with most other industrial fluid systems, leak-tight performance is essential. Achieving leak-free systems requires technicians to understand tube fitting and valve installation. Misunderstanding these essential steps in the process can cause critical fluid systems to fail, which can hamper the efficiency and effectiveness of a production facility.
System failures lead to unplanned downtime, decreased production, safety issues, and lower profitability. For these reasons, proper installation of leak-tight fluid systems in semiconductor manufacturing facilities is critical.
In addition to proper installation, designers and engineers must carefully consider how they route thermal loop lines. Hoses should be kept far enough away from each other, so the hoses’ surface temperatures do not fall below the dew point and cause condensation – or even icing.
The closer together the hoses are, the more likely they will cool the surrounding air to the chilled media’s temperature in the hose and cause condensation problems. A good rule of thumb is to keep hoses about 3X the diameter apart. If the configuration of the system does not allow such spacing, additional layers of insulation on the lines to maintain performance integrity may be required.
Stagnant air can also affect the surface temperature of cooling and heating lines. As airflow increases, surface temperatures can trend more toward the ambient environment temperature. Consider a hose that is routed through a confined area, such as a subfab. In the case of cold media flowing through the hose, this could cause condensation to form on the outside, which may drip onto sensitive equipment as discussed before.
Finally, while a hose’s minimum bend radius does not change when it is insulated, bending the hose may affect the insulation properties. To minimize these effects, it is generally recommended to make softer bends with a larger bend radius (Figure 4). If this is not possible, consider supplementing the hose with additional layers of insulation. See the sidebar to find out how to choose insulated hoses most effectively.
Building effective partnerships
As semiconductor manufacturing becomes increasingly important to the world economy, the race to lower costs has intensified. It is often difficult to trim costs on the expensive manufacturing tools that make high-quality chips possible to power future technological innovations. As a result, it makes sense to evaluate overall systems throughout the facility by looking for other less intrusive ways to lower manufacturing costs.
Evaluating whether the temperature-controlled fluid systems have the appropriate hoses is one such place to find unanticipated savings. Determining the precise level of necessary insulation can save money over time and help the system perform at peak efficiency over its lifespan – but operators, engineers, and technicians cannot be expected to know everything about thermal management. That is why finding a trusted supplier who can consult on these decisions is critical.
Finding a partner with the necessary experience in semiconductor manufacturing can provide valuable counsel about which components will meet the needs of particular applications. This guidance can mean reduced installation and operating expenses, improving profitability along the way. In the case of thermal loop components, an experienced partner can help determine how much insulation is necessary to keep chillers and other equipment operating properly. The more competitive the market becomes, the more important it will be to trim unnecessary expenses wherever possible.
The benefits of working with a supplier that can offer these tools and expertise can be significant, including:
• Reduced downtime via condensation prevention and less frequent maintenance
• Increased semiconductor chip yield via minimized thermal variation and efficient media transfer
• Increased efficiency and reduced energy costs via improved chiller performance
Maintaining optimal functionality of the thermal loop is essential to consistent, maximized chip yield in semiconductor wafer manufacturing settings. Work with a supplier who can dive deeply into specific applications and offer innovative solutions to semiconductor wafer manufacturing operations. Find a partner with broad reach who can not only advise on proper hose choices but other components as well. Working together, semiconductor fabs can keep moving the world forward and running smoothly as technology continues to improve.